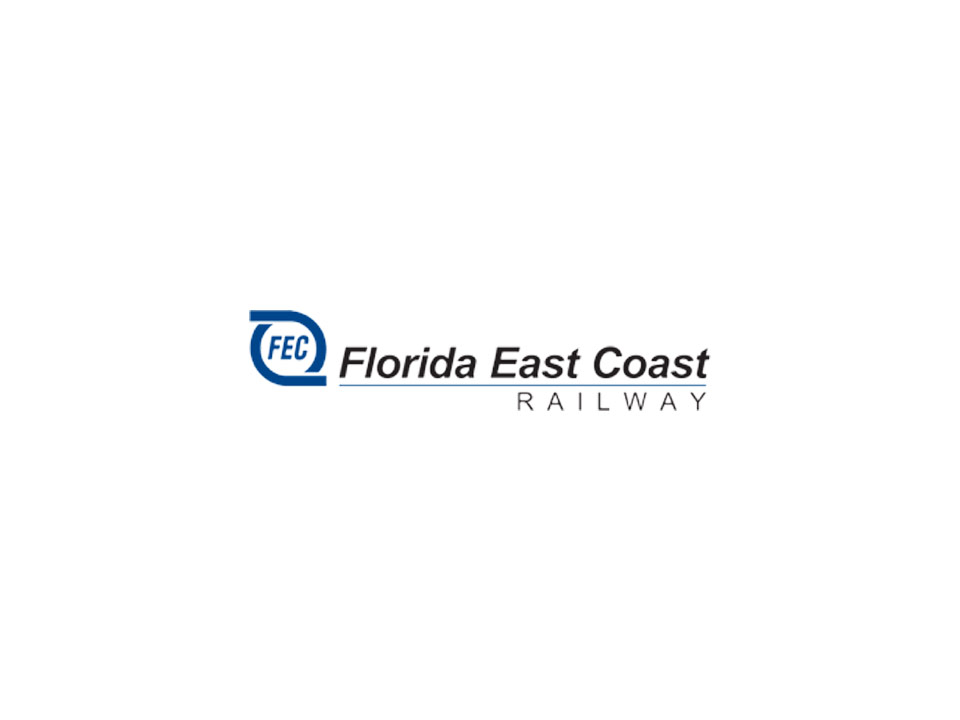
Florida East Coast Earns American Honda’s ‘Performance Excellence’ Award
September 7, 2011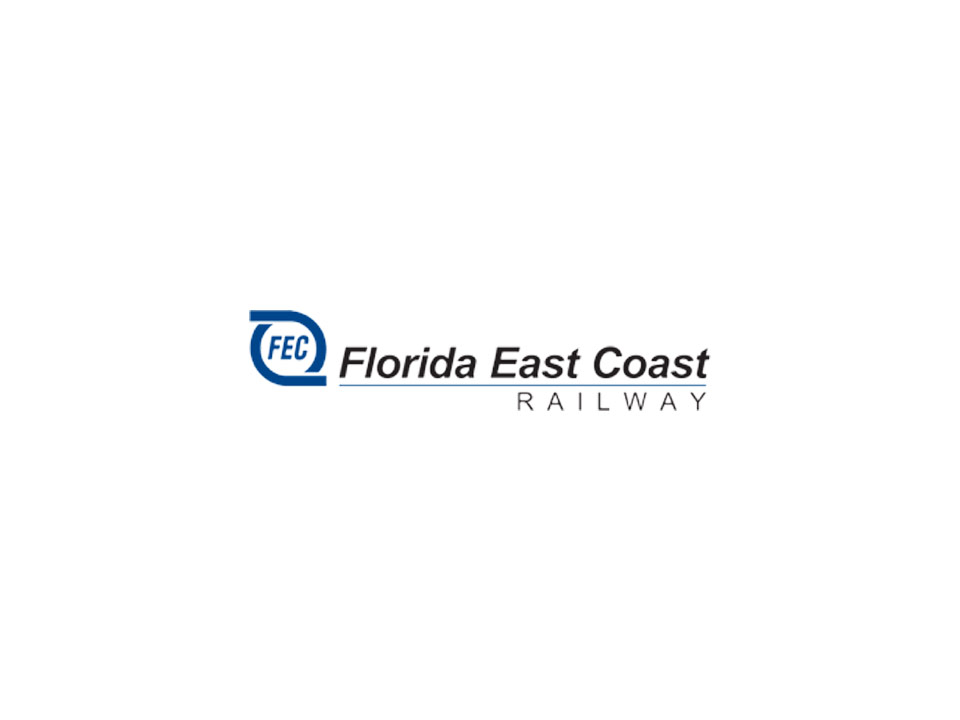
Industry Forum for Port of Miami Bascule Railroad Bridge Rehabilitation
September 15, 2011For Maintenance-of-Way Managers, Finding Ways to Boost Productivity is Key
"Git 'er done." Comedian Larry the Cable Guy's grammatically incorrect, but popular catchphrase accurately describes maintenance-of-way (MOW) managers' charge throughout 2011. They're trying to complete all planned trackwork and capacity expansion projects for their respective freight or passenger railroads by year's end despite the usual challenges of tight budgets and narrow work windows.
This year, managers also are facing a couple of not-so-typical hurdles: a volatile economy that's placing every MOW expenditure under the budgetary microscope, and an erratic Mother Nature that's produced infrastructure-damaging floods and tornadoes, which are straining department resources.
So far, BNSF Railway Co. is managing to overcome most of the obstacles to its MOW program, including spates of severe weather. Since March, massive flooding in parts of the nation has prompted the railroad to divert crews and equipment from ongoing project sites.
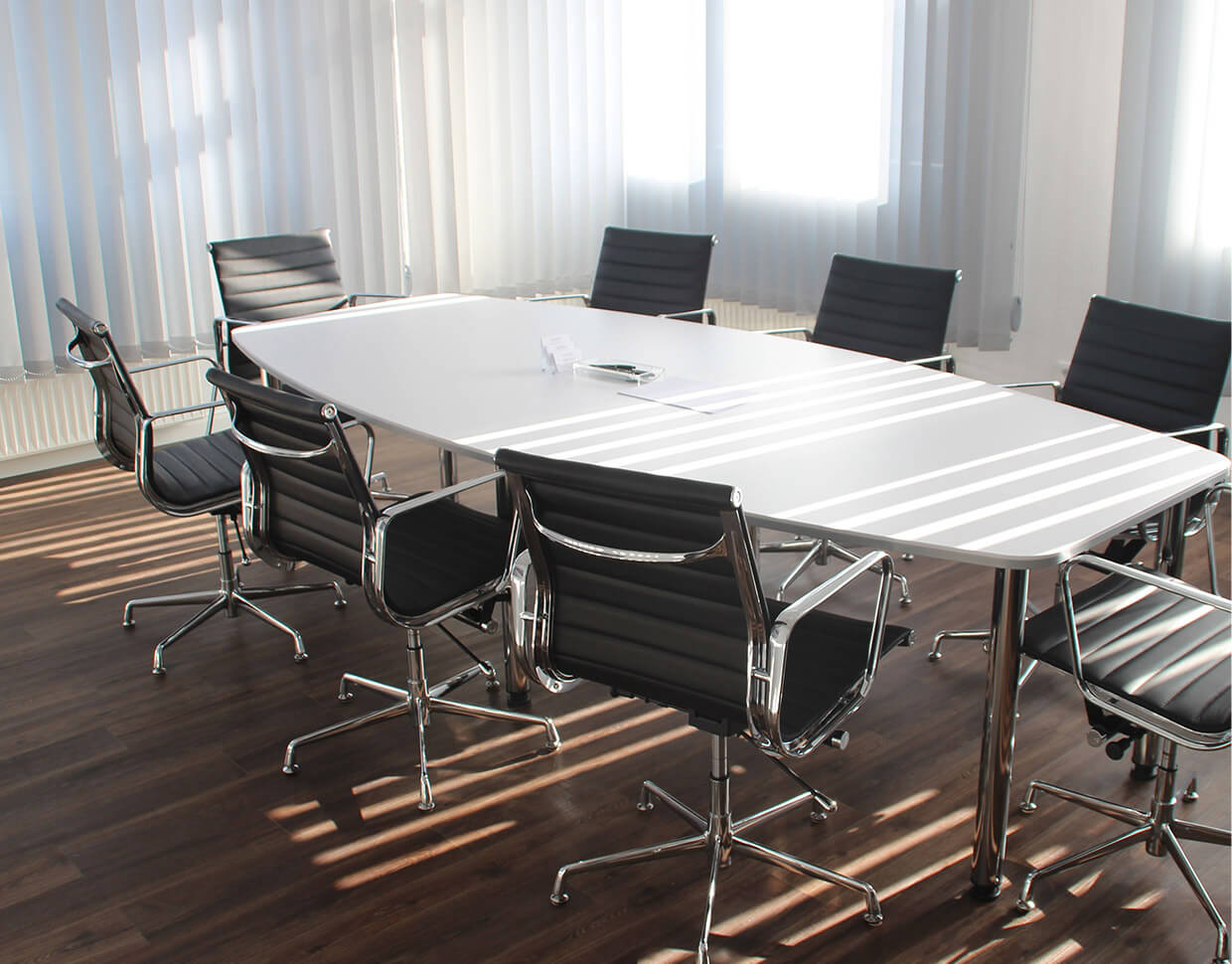
Recent Creston Subdivision flooding in Nebraska and Iowa required BNSF to raise two mainline tracks up to eight feet and build levees six feet above the top of the rail to keep a line in service. As of mid-August, similar work was under way or set to begin in subdivisions touching parts of Missouri, Montana and North Dakota.
But flood-related repairs — which are expected to continue into October — haven't thrown the MOW program off schedule, says BNSF Assistant Vice President and Chief Engineer of System Maintenance Bill Van Hook.
The engineering department has outsourced some preventative and restoration work to contractors, and the transportation department has provided necessary work windows to "progress the capital improvements planned during this difficult period," he says.
"We still expect to complete most of the [program] work by early December," says Van Hook.Major projects continue to meet timelines, as well, such as the completion of seven miles of double track in New Mexico's Abo Canyon in early June. The project — which called for laying five miles of new track, blasting about 3.6 million tons of rock and building nine bridges totaling 3,000 feet in length — was "by far" the largest and most expensive in this year's program, says Van Hook.
"We'll have to do that mostly by being more productive," he says.
When it comes to completing programs on budget and on time — no matter the obstacles — finding more ways to boost productivity is key, MOW managers say. To gain maximum output from crews and equipment, they're trying to employ more productive machinery, implement more efficient work processes, or install components and materials that better suit today's get-it-done-quickly demands.

Material Evidence
At Wisconsin & Southern Railroad Co. (WSOR), a track component change is paying off in enhanced productivity. Instead of installing wood tie plugs as the regional did in the past, WSOR now is using liquid chemical plugs that are pushed into cracks to better seal a tie. It only takes three workers to install the liquid chemical plugs compared with six to manually plug ties, says Superintendent of Maintenance Ben Meighan. "We are also concerned about repetitive motion injuries, which can be reduced with the chemical applicator," he says.
Florida East Coast Railway L.L.C. (FEC) is boosting productivity by using a different component, too. As part of this year's MOW program, crews for the first time are installing Rocla Concrete Tie Inc. ties with Vossloh Fastening System fasteners already attached. The concrete ties are inserted under rail like wood ties, says FEC Vice President and Chief Engineering Officer Robert Stevens. "This enables us to use two less machines in gangs and use nine workers instead of 12 with the same productivity and completion of a typical tie program," he says, adding that there's also less hindrance on operations because less ballast is disturbed.
FEC also is registering efficiency gains from a piece of machinery. Crews continue to use Harsco Rail's Mud Mantis spot undercutter, which can return 75 percent of ballast after undercutting operations, says FEC's Stevens. Ballast removed by an undercutter bar and digging wheel can be conveyed either to a vibratory shaker or spoil conveyor system. The shaker is designed to separate ballast by size; over- or under-size material is removed and routed to a spoil conveyor system while desired-size, cleaned ballast is returned to the track.
Likewise, better efficiency is the main reason three Class Is are employing a recently developed piece of equipment: a "drone" chase tamper marketed by Harsco Rail. The unmanned tamper is designed to receive signals wirelessly from sensors on the lead tamper to determine which ties to tamp. The drone tamper can be programmed to tamp every other tie or third tie. NS currently is using a few drone tampers and expects to have five on hand by year's end. The machine eliminates tamping production "difficulties" posed by missing ties, says NS Vice President of Engineering Tim Drake.
"We also save on labor and gain safety," he says. Last year, the engineering department logged a record 0.5 safety ratio — based on the number of injuries per 200,000 manhours — the lowest ratio among all NS departments, says Drake, adding that this year's ratio is trending below 0.5. CN is using drone tampers, as well. The Class I acquired three units this year and plans to take delivery of three more in January 2012. Crews use the drones in combination with Mark IV units to boost those tampers' productivity, says CN VP of System Engineering David Ferryman.

Material Evidence
At Wisconsin & Southern Railroad Co. (WSOR), a track component change is paying off in enhanced productivity. Instead of installing wood tie plugs as the regional did in the past, WSOR now is using liquid chemical plugs that are pushed into cracks to better seal a tie. It only takes three workers to install the liquid chemical plugs compared with six to manually plug ties, says Superintendent of Maintenance Ben Meighan. "We are also concerned about repetitive motion injuries, which can be reduced with the chemical applicator," he says.
Florida East Coast Railway L.L.C. (FEC) is boosting productivity by using a different component, too. As part of this year's MOW program, crews for the first time are installing Rocla Concrete Tie Inc. ties with Vossloh Fastening System fasteners already attached. The concrete ties are inserted under rail like wood ties, says FEC Vice President and Chief Engineering Officer Robert Stevens. "This enables us to use two less machines in gangs and use nine workers instead of 12 with the same productivity and completion of a typical tie program," he says, adding that there's also less hindrance on operations because less ballast is disturbed.
FEC also is registering efficiency gains from a piece of machinery. Crews continue to use Harsco Rail's Mud Mantis spot undercutter, which can return 75 percent of ballast after undercutting operations, says FEC's Stevens. Ballast removed by an undercutter bar and digging wheel can be conveyed either to a vibratory shaker or spoil conveyor system. The shaker is designed to separate ballast by size; over- or under-size material is removed and routed to a spoil conveyor system while desired-size, cleaned ballast is returned to the track.
Likewise, better efficiency is the main reason three Class Is are employing a recently developed piece of equipment: a "drone" chase tamper marketed by Harsco Rail. The unmanned tamper is designed to receive signals wirelessly from sensors on the lead tamper to determine which ties to tamp. The drone tamper can be programmed to tamp every other tie or third tie. NS currently is using a few drone tampers and expects to have five on hand by year's end. The machine eliminates tamping production "difficulties" posed by missing ties, says NS Vice President of Engineering Tim Drake.
"We also save on labor and gain safety," he says. Last year, the engineering department logged a record 0.5 safety ratio — based on the number of injuries per 200,000 manhours — the lowest ratio among all NS departments, says Drake, adding that this year's ratio is trending below 0.5. CN is using drone tampers, as well. The Class I acquired three units this year and plans to take delivery of three more in January 2012. Crews use the drones in combination with Mark IV units to boost those tampers' productivity, says CN VP of System Engineering David Ferryman.
A Moveable Object
Count several passenger railroads among the users — and seekers — of more productive equipment. In fall, Amtrak plans to take delivery of a self-contained mobile workstation manufactured by ROBEL in Germany that's predominantly used in Europe. Resembling a hollowed-out rail car, the workstation can reduce assembly and dismantling time because it can be customized for specific tasks — such as electric arc or thermite welding, or pad and clip change-outs — and shelter workers from wind and inclement weather, says Amtrak Chief Engineer Frank Vacca.
The workstation also can protect crews from passing trains on adjacent tracks, boosting roadway safety, he says.Amtrak plans to test it in the Philadelphia/New York City region. The railroad might acquire more workstations if they perform well during tests, says Vacca.If funding is available in the FY2012 budget, Amtrak also might purchase a wire replacement machine used in Europe to replace multiple catenary wires at a time. In FY2012, the railroad plans to replace 90-year-old catenary along 230 miles between New York City and Washington, D.C., where in certain areas, three, four or more tracks are in place.
"Right now, we can only replace one wire at a time," says Vacca. "We can be more productive by replacing two or three wires at a time." MTA Metro-North Railroad already is replacing catenary. The railroad is carrying out an ongoing, multi-phased project funded by the state of Connecticut that calls for replacing 20 miles of catenary and five bridges.
Time Is Of The Essence
In terms of equipment, Metro-North also has "taken a look" at ROBEL's mobile workstation, says Director of Track and Structures John Wagner. For now, the railroad has purchased a Loram Maintenance of Way Inc. RAILVAC™ excavator it's leased for seven years because the machine can be used year round, he says. Instead of just using the RAILVAC for undercutting or removing fouled ballast during trackwork months, Metro-North crews can use it to pick up trash at station areas any time, says Wagner..
LIRR also might make an equipment purchase in the near term. The railroad is determining whether to buy a Jordan Spreader manual plow because of this past winter's heavy snowfalls, says LIRR's Puciloski. A Jordan Spreader is coupled to a locomotive and controlled by an engineer in the cab. While he contemplates the equipment purchase, Puciloski also is considering a work item addition to LIRR's next MOW program: a grinding campaign.
"The last grinding program we did was seven years ago, and it always falls by the wayside," he says. "In a couple of years, we could get the whole system grinded." At NS, crews are making some progress with a work item goal. The Class I aims to remove more joints from its network, primarily by installing more flash-butt welds, which are stronger and can last longer than thermal welds.
At the start of 2010, there were more than 18,000 joints in the network, which months later were whittled down to 9,000, then increased back to 10,000 because of rail damage caused by a "tough winter," says NS' Drake. By 2011's end, the number should drop to 7,500, he says.
The Place To Be
CN also is analyzing a plate machine designed to place tie plates ahead of a surfacing gang to speed that work process. "It's all about eliminating steps in production gangs — that's a place we want to be," says Ferryman. Ditto for BNSF. The Class I is employing two drone tampers and might use more in the future, says BNSF's Van Hook.
In addition, the Class I continues to expand its usage of ground penetrating radar (GPR) to more accurately undercut and clean shoulder ballast. This year, GPR will be employed on 4,000 of the 14,500 miles of track that need the ballast work; next year, crews will use the technology on more track miles, says Van Hook.
BNSF also plans to increase its usage of Plasser American Corp.'s 09-32 DYNA-CAT high-speed, continuous-action tamper. The Class I employs three of the production tampers and expects to take delivery of a fourth in fall, says Van Hook. The machine features 32 tools and built-in stabilizers, and can tamp two ties at a time vs. the one-tie capacity of Plasser's 09-16 DYNA-CAT.
Earlier this year, CN acquired four 09-32 DYNA-CATs, and the railroad plans to acquire two more in 2012. The production tampers are used by seven-member super surfacing gangs, which the Class I formed to conduct more program surfacing work than in years past.
Seeking A Software Assist
BNSF is posting progress with a MOW goal, too. An ongoing effort centers on the development of the Engineering Asset Manager (EAM), a back-office computer system designed to consolidate all engineering data. EAM's five-year development program began this year and pieces of the system will be rolled out in 2012, said BNSF's Van Hook.
"Now, all physical plant data is in different programs, and we want all data to reside in one place," he says. "We can gain efficiency and track costs against any single asset we want to identify."A few other railroads already have notched efficiency gains and other operational benefits from MOW projects completed earlier this year.
WSOR removed 2,000 feet of track and all fouled ballast in Waukesha, Wis., then rebuilt the track on new ballast and corrected an alignment problem, including three grade crossings. Track was shifted up to two feet to make multiple tracks work as a connection."The old alignment was not good for today's needs [because] our trains are getting longer than anticipated," says WSOR's Meighan. "In the old days, our trains were 40 cars long; today they average 125-plus cars and we recently had one 11,000 feet long."
.Meanwhile, FEC relocated an auto facility from the south end to north end of Hialeah Yard in Miami to free up land for the development of a logistics park; CN extended 6,000- to 6,900-foot sidings in northern Ontario to 12,000 feet, and planned to lengthen a few more sidings by year's end to accommodate longer trains; Metro-North closed a bridge in Mount Vernon, N.Y., for six weeks to perform priority repairs and modernize the 62-foot-long, 117-year-old structure; and NS completed three months' worth of trackwork in eight early July days on a southwestern Pennsylvania coal route to take advantage of coal miners' annual summer break and impact train operations as minimally as possible during construction.
While railroads continue to carry out a number of projects in 2011 designed to boost productivity and efficiency, available work windows remain paramount because of rising traffic volumes, MOW managers say.Track time and productivity undoubtedly will be a key issues in 2012, as well. At NS, for example, managers have set train delay elimination goals."We are trying to shave minutes off of delays," says NS' Drake.And when it comes to meeting project and train schedules — as well as ensuring all MOW goals are fulfilled — every minute counts.